Overview of Stock Management
Stayflexi’s Stock Management system helps properties track and manage their inventory, orders, and suppliers. It offers tools to monitor stock levels in real time, create purchase orders, and receive alerts for low stock. This system helps reduce waste, improve efficiency, and keep operations running smoothly, particularly in the hospitality industry.
Stock management consists of the following option:
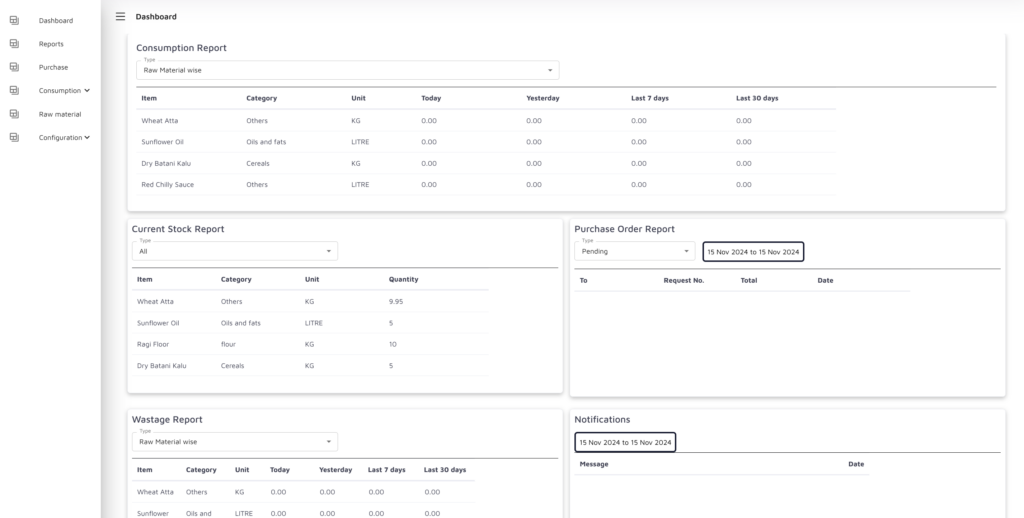
- Dashboard:
- The Dashboard consists of the following options:
- Consumption Report: Shows real-time data on the usage of raw materials.
- Current Stock Report: Provides an overview of stock levels for each item.
- Purchase Order Report: Lists pending and recent purchase orders.
- Wastage Report: Displays wastage data to help control costs and minimize losses.
- Notifications Column: Centralized alerts for stock status.
- The Dashboard consists of the following options:
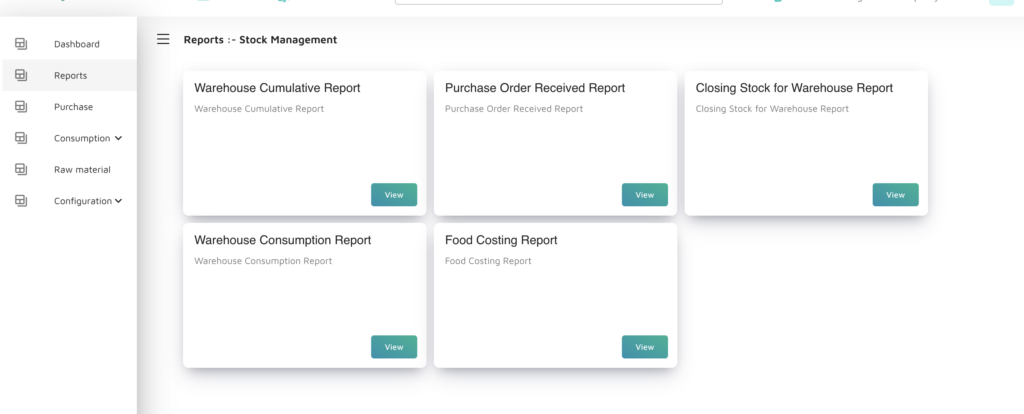
- Reports:
- The Reports consist of the following reports:
- Warehouse Cumulative Report: Provides an overall summary of warehouse stock and activities.
- Purchase Order Received Report: Displays details of purchase orders received by the warehouse.
- Closing Stock for Warehouse Report: Shows the closing stock levels for the warehouse at the end of a specified period.
- Warehouse Consumption Report: Tracks the consumption of stock in the warehouse.
- Food Costing Report: Analyzes the cost breakdown of food-related inventory.
- The Reports consist of the following reports:
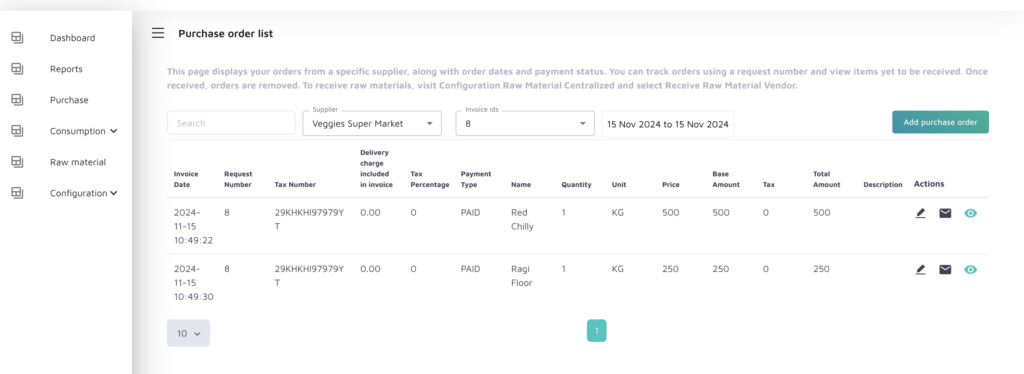
- Purchase:
- This page displays your orders from a specific supplier, along with order dates and payment status.
- You can track orders using a request number and view items yet to be received. Once received, orders are removed.
- Consumption:
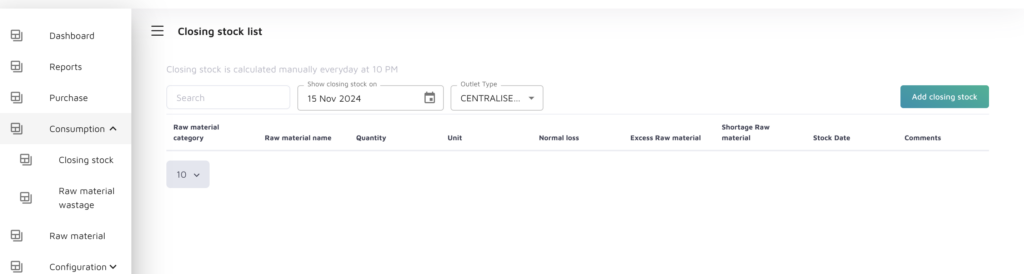
- Closing stock:
- The Closing Stock feature in Stayflexi enables properties to track and record end-of-day inventory levels for raw materials, ensuring accurate stock management across various categories and outlets. Users can select a date, outlet type, and raw material category, then input specific quantities and units for each item in stock.
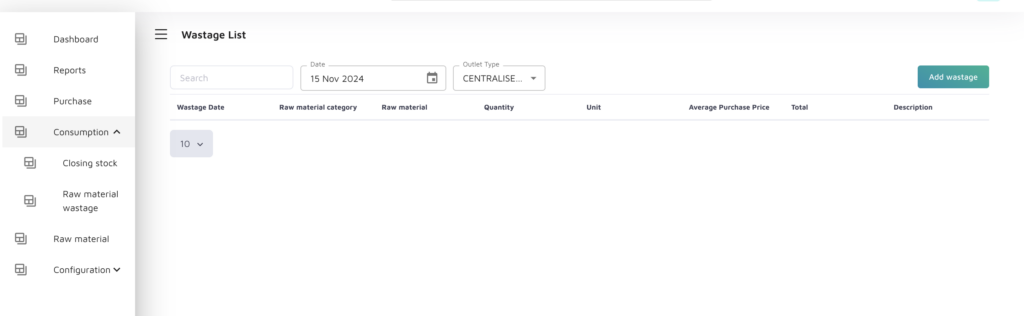
- Raw material wastage:
- The Raw Material Wastage option in stock management is a feature that helps businesses track and manage the loss or spoilage of raw materials. In any inventory system, wastage can occur due to various reasons such as spoilage, expiration, handling errors, or production processes.
- Overall, this feature aids in minimizing waste, optimizing stock levels, and ultimately lowering operational costs by providing clear insights into how raw materials are used and where losses occur.
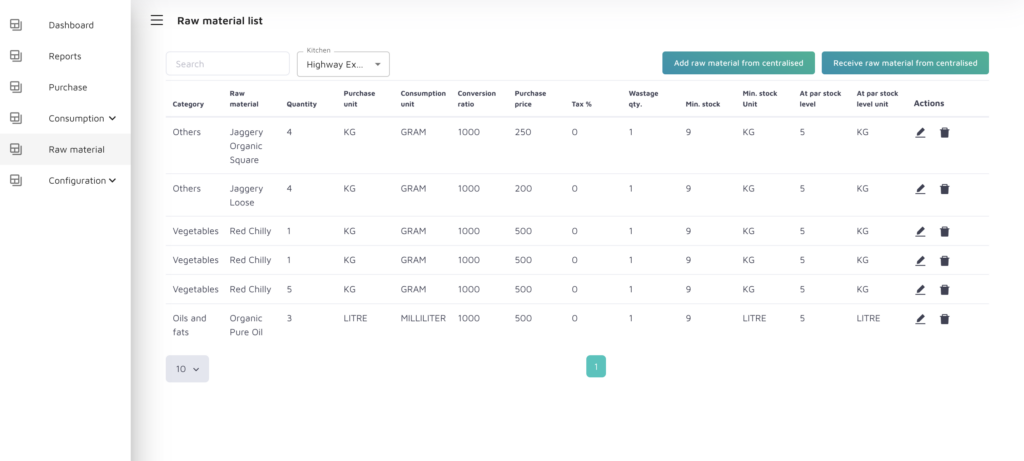
- Raw material:
- The Raw Material in stock management allows efficient tracking of inventory by category, showing details like quantity, units, conversion ratio, and stock levels. Users can manage costs, monitor wastage, and update inventory easily with options to add, receive, edit, or delete items from a centralised stock.
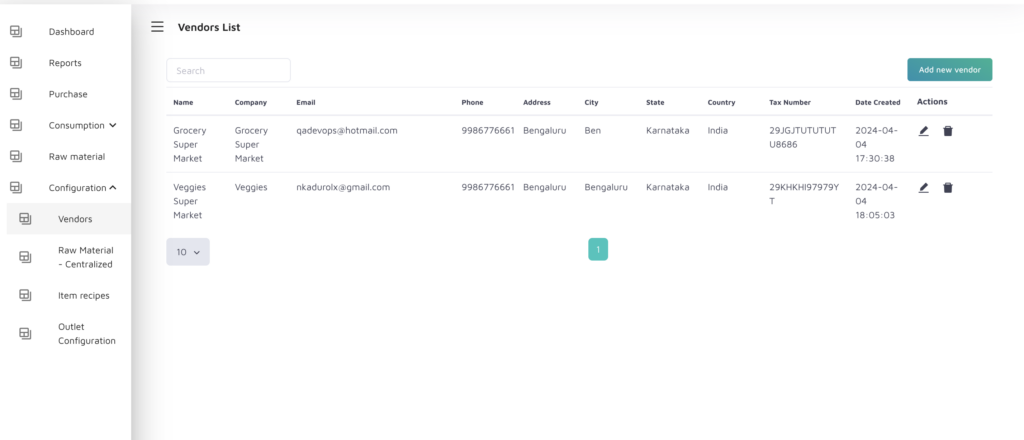
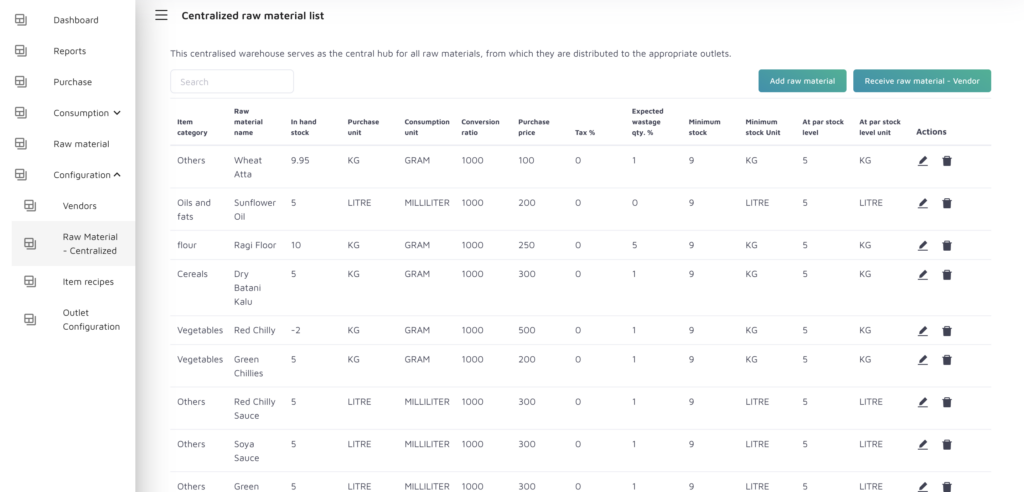
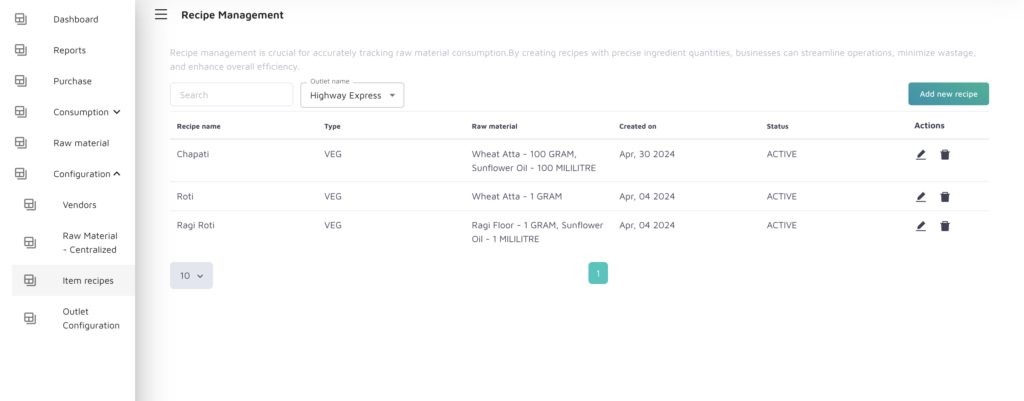
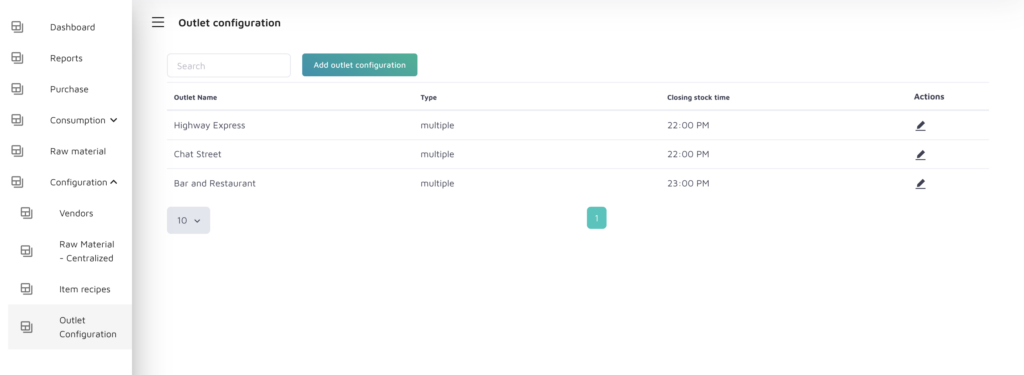
- Configuration:
- The Configuration includes:
- Vendors: Stores information about suppliers, making it easier to order materials from trusted vendors.
- Raw materials – Centralised: This centralised warehouse serves as the central hub for all raw materials, from which they are distributed to the appropriate outlets.
- Item recipes: By creating recipes with precise ingredient quantities, businesses can streamline operations, minimise wastage, and enhance overall efficiency.
- Outlet configuration: To ensure easy configuration with a specific shop and effective tracking of raw material data, it is recommended that the outlet be named the same as the shop.
- The Configuration includes: